Isolating Particle Splatter in CSAM
For my capstone project, I worked on a small team to develop a research tool for Northeastern’s Additive Manufacturing Lab. Our advisor wanted a device that could separate individual layers of particle buildup in cold spray additive manufacturing (CSAM) so that he could more closely study how deposits form. Being able to study this would allow for the development of more effective tools and powders in CSAM. To build a successful device, we had to make sure it could separate particle streams moving at roughly 1,000m/s, with at least 2.5 particle diameters of space between each splat. The device also needed to be controlled from outside of the spray chamber and had to be able to run 5-10 samples at once.
My main responsibility for the project was to design and fabricate the mechanical system. After we settled on a design concept, I used SolidWorks to develop a model of the design. Using this model and the drawings I prepared, I communicated with our school’s machine shop to have each part manufactured. After running into some problems during our initial test, we needed a few new parts but didn’t have time to go through the machining process. To deal with this issue, I had to redesign the parts to make them using a 3D printer.
After the final test we analyzed the samples. Just looking at them it was clear that we were able to create isolated splats, but it wasn’t until we examined them under a high-powered microscope that we were able to see the degree of particle separation. In addition, there were several dimples, or cavities caused by particles bouncing off the substrate rather than bonding to it. Our advisor was very happy to see these results so at that point we handed the project over to him for any final tweaking and programming.
Design and Build
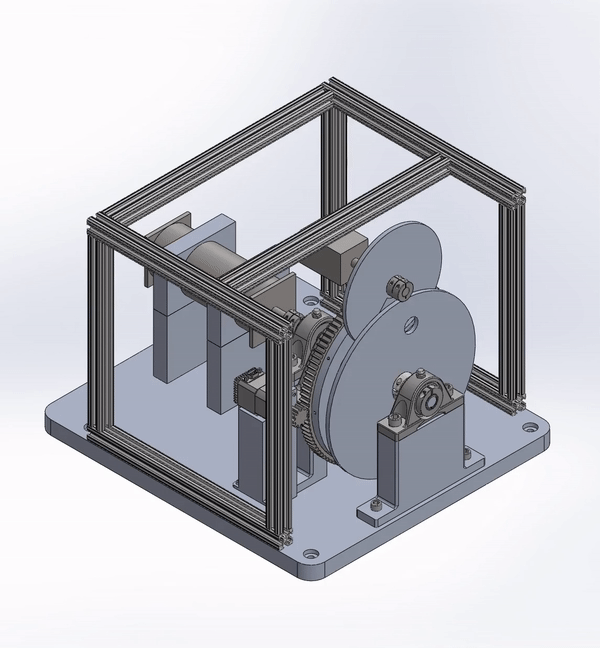

Testing and Results
